The LEGO Super Mario line has been immensely popular with kids and even some adult LEGO fans. The Mario figure in the #71360 LEGO Super Mario Adventures with Mario Starter Course is a marvel of engineering with its color sensors, LCD screens in his eyes, mouth, and belly to display over 100 different instant reactions to movement, and a speaker that plays iconic sounds and music from the video game. And there are also a bunch of add-on sets that allows you to add extra characters, enlarge the course, and enhance Mario’s capabilities. You can read more about the sets here: LEGO Super Mario Sets Overview
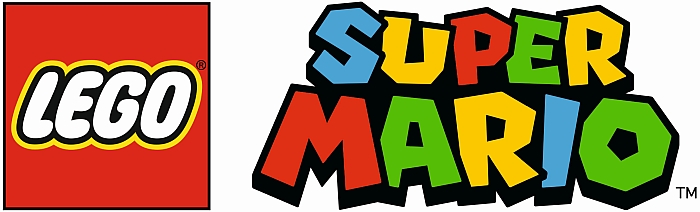
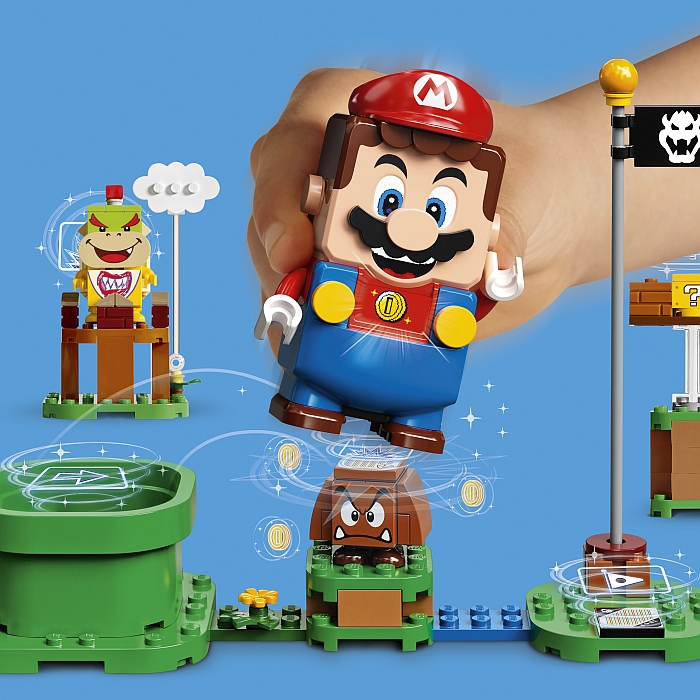
A couple of days ago, the LEGO Group and Nintendo announced that they are going to release even more LEGO Super Mario sets next year for customized adventures, including the LEGO Super Mario Master Your Adventure Maker Set, which puts kids in charge of the interactive level play like never before, three new LEGO Super Mario Expansion Sets, two new LEGO Super Mario Power-Up Packs, and ten new LEGO Super Mario Collectible Character Packs. Below is the press-release with more information:
BILLUND, November 17, 2020: The LEGO Group today announced a brand new range of sets and characters, opening up even more new adventures for the LEGO Super Mario experience. Fans can expand on the LEGO Super Mario products launched earlier this year with a whole new range of sets and Collectible Characters – all designed to help them build a Super Mario world that’s unique to them and comes alive exactly how they want it to.
Among the new sets is the Master Your Adventure Maker Set – a creative toolbox, which enables children to completely customize LEGO Super Mario building, play time, and ways to earn coins. Using the Customization Machine included in the Maker Set, children can change how LEGO Mario reacts to three Special Bricks, offering variety in play, excitement and an element of surprise. The Maker Set also introduces a new special Start Pipe that will shuffle the known rules of the level play, in that players are challenged to reach the Goal Pole in less time, yet with increased rewards up for grabs. The Maker Set comes with 366 pieces; all selected to ensure that children can unleash their creativity and customize their own levels for themselves or other players.
The other sets introduced today are the Chain Chomp Jungle Encounter Expansion Set, the Piranha Plant Puzzling Challenge Expansion Set, the Wiggler’s Poison Swamp Expansion Set, Penguin Mario Power-Up Pack, and the Tanooki Mario Power-Up Pack.
Also announced today is Series 2 of the LEGO Super Mario Character Packs, all featuring an action tag that LEGO Mario can read for fans to easily integrate into the level play. Series 2 features ten brand new collectible, buildable characters. Kept a surprise until opened, fans could be getting a Huckit Crab, Spiny Cheep Cheep, Ninji, Foo, Parachute Goomba, Fly Guy, Poison Mushroom, Para-Beetle, Thwimp, or a Bone Goomba.
The new sets and characters will give fans the chance to, among other things, have LEGO Mario slide on his belly as Penguin Mario, or spin round as Tanooki Mario. The sets will also introduce much-loved enemies including the Piranha-Plants, Larry, a Goomba, Wiggler, and Koopa Paratroopa, to the play, all of who can be defeated or played with for coin rewards.
LEGO Super Mario jumped into existence earlier this year through a unique partnership between the LEGO Group and Nintendo. The adventures were kick-started with an entry-point set: LEGO Super Mario Starter Course, which includes an interactive LEGO Mario figure that collects coins in interactive level play created with LEGO bricks. Each Expansion Set and Collectible Character is designed to be used with the entry point set, featuring seven action bricks for different interactions with the LEGO Mario figure, which has LCD screens in its eyes, mouth, and belly to display instant reactions to movement, color, and action bricks. Building on the existing biomes of water (blue), fire (red), sand (yellow), and grass (green), this second wave of products introduces Soda Jungle, a whole new biome characterized by its purple color, which represents poison, that enables children to experience different reactions from LEGO Mario and new ways of playing.
All sets and characters are compatible, allowing fans to combine sets and characters announced today with the Starter Course and all other LEGO Super Mario products revealed in June this year. All sets come with their own series of distinctive challenges and characters, and have also been designed to work alongside the free LEGO Super Mario app, so fans can make the most of the experience when playing solo, or when challenging friends or family members. The app hosts 3D building instructions for the sets, keeps track of scores, and provides inspiration for builds and ways of playing to encourage continuous rebuilding and extended playtime.
“It wouldn’t be Super Mario if we weren’t constantly creating new worlds and adventures for everyone’s favorite Plumber,” said Simon Kent, Design Director and Creative Lead for LEGO Super Mario, the LEGO Group. “The LEGO Super Mario sets we released earlier this year have been extremely well-received by fans and we’re really excited to build on those with even more characters and experiences today. We really want to empower users to be as creative as possible with LEGO Super Mario – and today’s expansion sets and new collectible characters have been launched to broaden the horizons of the LEGO Super Mario universe, letting players be as imaginative as possible in the way they have Mario interact with his friends – as well as defeating his enemies.”
The new Sets and Character Packs will launch on January 1st, 2021 across LEGO brand retail stores, the Online LEGO Shop, and from select leading retailers around the world. The recommended retail price for the sets are as follows:
- #71380 LEGO Super Mario Master Your Adventure Maker Set (366 Pieces): 59.99 USD/EUR – 49.99 GBP – 89.99 AUD – 69.99 CAD
- #71381 LEGO Super Mario Chain Chomp Jungle Encounter Expansion Set (160 Pieces): 19.99 USD/ 24.99 EUR -19.99 GBP – 39.99 AUD – 24.99 CAD
- #71382 LEGO Super Mario Piranha Plant Puzzling Challenge Expansion Set (267 Pieces): 29.99 USD/EUR – 24.99 GBP – 49.99 AUD – 39.99 CAD
- #71383 LEGO Super Mario Wiggler’s Poison Swamp Expansion Set (374 Pieces): 39.99 USD/EUR – 34.99 GBP – 59.99 AUD – 49.99 CAD
- #71384 LEGO Super Mario Penguin Mario Power-Up Pack (18 Pieces): 9.99 USD/EUR – 8.99 GBP – 12.99 AUD – 13.99 CAD
- #71385 LEGO Super Mario Tanooki Mario Power-Up Pack (13 Pieces): 9.99 USD/EUR – 8.99 GBP – 12.99 AUD – 13.99 CAD
- #71386 LEGO Super Mario Character Packs – Series 2: 4.99 USD/3.99 EUR – 3.49 GBP – 5.99 AUD – 4.99 CAD
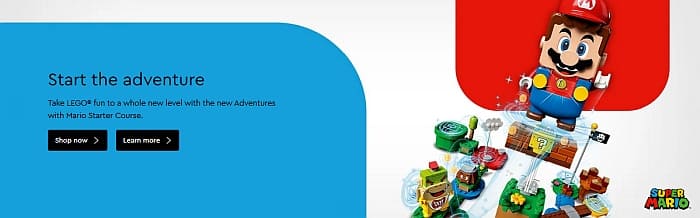
It seems like LEGO is committed to continue the LEGO Super Mario theme with some great additions that should please fans. And while we are waiting, you can check out the currently available sets in the LEGO Super Mario section of the Online LEGO Shop.
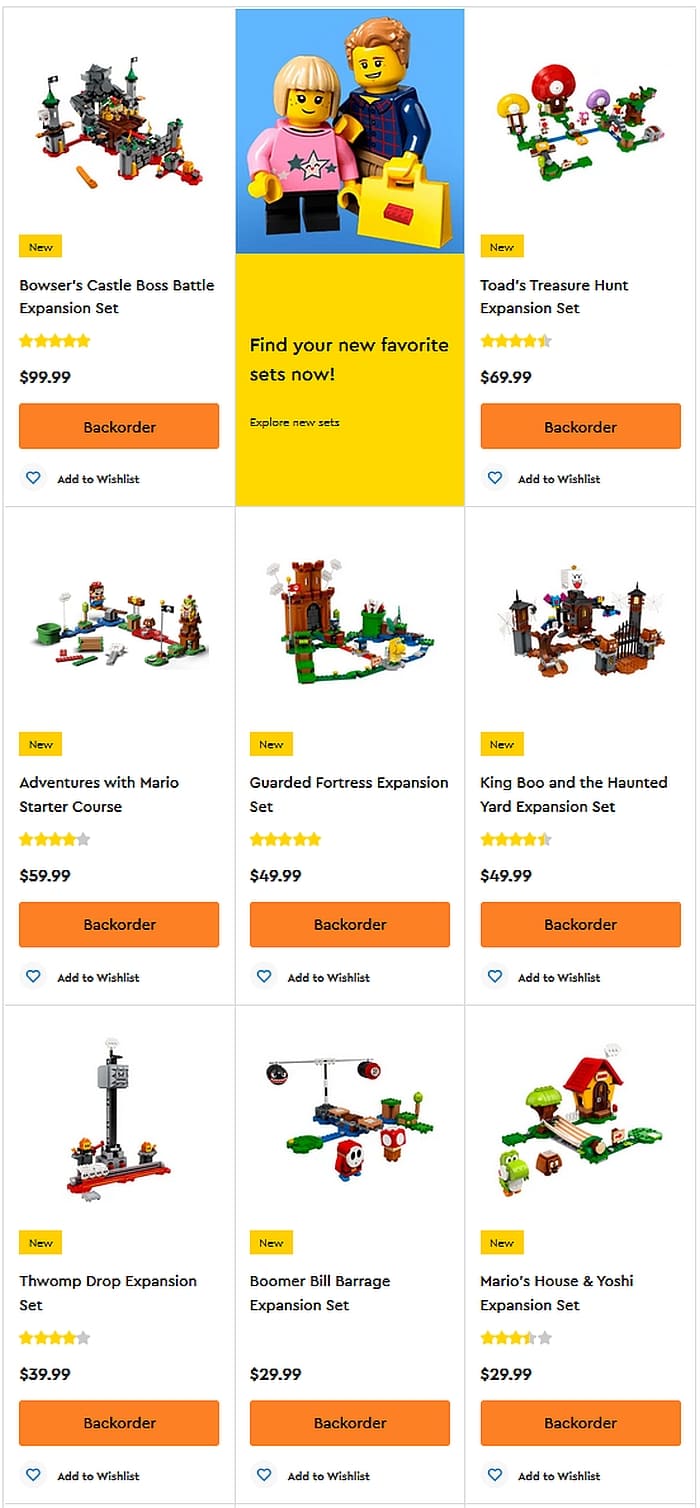
What do you think? How do you like the currently available LEGO Super Mario sets? Do you have any of them already? And what do you think of the sets coming next year? Feel free to share your thoughts and discuss in the comment section below!
And you might also like to check out the following related posts: